Define an Internal Force Constraint in Tosca ANSA® environment
To create a constraint, select on CONSTRAINTS item.
Choose TARGET
= NODE_AND_ELEMENT_GROUP, ND_GROUP_DEF = ND_GROUP_DEF, EL_GROUP_DEF
= EL_GROUP_DEF.
Press "?" key in ND_GROUP_DEF
field and choose the appropriate node group.
Repeat for EL_GROUP_DEF
where an element group shall be chosen, see the following figure.
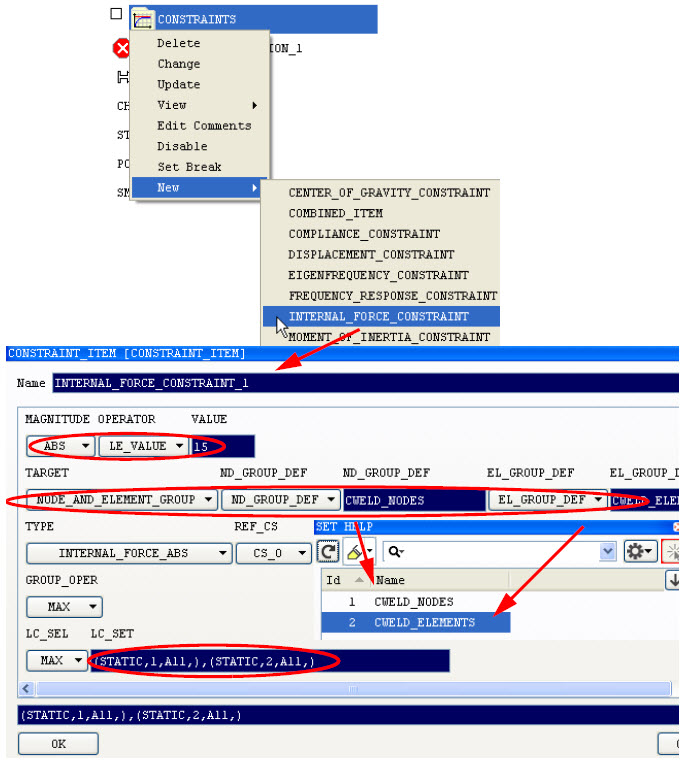
Internally in SIMULIA Tosca Structure,
a separate design response for each pair (node, element) is created,
where the node belongs to the chosen node group and to the element (that
itself belongs to the chosen element group). In the example, 32 nodes
are connected to the cweld elements. Since there are two load cases,
64 design responses are produced in SIMULIA Tosca Structure.

Define an Internal Force Constraint in Tosca Structure.gui
- Define an internal force constraint in Tosca Structure.gui as shown in the following figure:
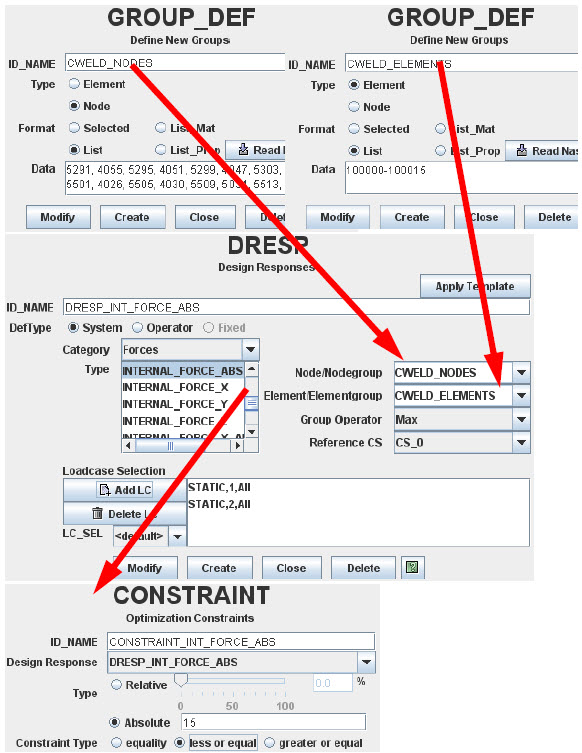

Define a Reaction Force Constraint in Tosca Extension for ANSYS® Workbench
Before you begin: Internal forces are not available in the Tosca Extension for ANSYS® Workbench
and thus the setup is performed using reaction forces.
To define a Reaction Force constraint within a Design
Response, add a Design Response first
by clicking .
Select
Reaction Force/Moment as Category and
the desired direction as Response Type;:
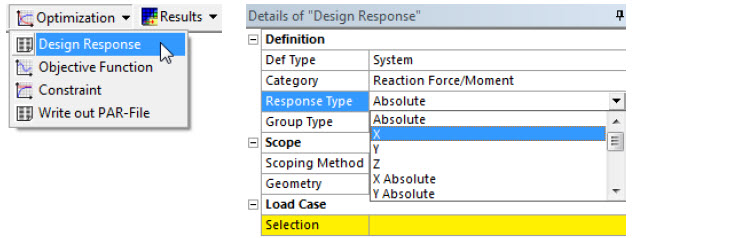
Assign a node to the design response.
Call this Design Response in a Constraint.
Therefore add a Constraint
to the project first, by clicking .

Result and Convergence Objective function plot (relative material volume) is presented in the next figure:
Internal force constraint values are pictured in the following figure:
Displacement constraint values are shown in the next figure:
The last figure presents the result of the optimization under force constraints in the spot weld elements:
SIMULIA Tosca Structure Parameter File
- The commands in the parameter file look like follows:
DRESP
ID_NAME = DRESP_VOLUME
TYPE = VOLUME
DEF_TYPE = SYSTEM
GROUP_OPER = Sum
EL_GROUP = ALL_ELEMENTS
END_
OBJ_FUNC
ID_NAME = MINIMIZE_VOLUME
TARGET = MIN
DRESP = DRESP_VOLUME, ,
END_
GROUP_DEF
ID_NAME = CWELD_NODES
TYPE = NODE
FORMAT = LIST
LIST_BEGIN
5291, 4055, 5295, 4051, 5299, 4047, 5303, 4043,
5501, 4026, 5505, 4030, 5509, 4034, 5513, 4038,
5186, 4685, 5190, 4681, 5194, 4677, 5198, 4673,
5396, 4656, 5400, 4660, 5404, 4664, 5408, 4668
END_
GROUP_DEF
ID_NAME = CWELD_ELEMENTS
TYPE = ELEM
FORMAT = LIST
LIST_BEGIN
100000-100015
END_
DRESP
ID_NAME = DRESP_INT_FORCE_ABS
TYPE = INTERNAL_FORCE_ABS
DEF_TYPE = SYSTEM
GROUP_OPER = Max
EL_GROUP = CWELD_ELEMENTS
ND_GROUP = CWELD_NODES
END_
CONSTRAINT
ID_NAME = CONSTRAINT_INT_FORCE_ABS
DRESP = DRESP_INT_FORCE_ABS
MAGNITUDE = ABS
LE_VALUE = 15
END_
DRESP
ID_NAME = DRESP_DISP_LC11
DEF_TYPE = SYSTEM
TYPE = DISP_ABS
NODE = 3900
LC_SET = ALL,11,All
GROUP_OPER = Max
END_
DRESP
ID_NAME = DRESP_DISP_LC12
DEF_TYPE = SYSTEM
TYPE = DISP_ABS
NODE = 4530
LC_SET = ALL,12,All
GROUP_OPER = Max
END_
CONSTRAINT
ID_NAME = MAX_DISP_LC11
MAGNITUDE = ABS
DRESP = DRESP_DISP_LC11
LE_VALUE = 0.003
END_
CONSTRAINT
ID_NAME = MAX_DISP_LC12
MAGNITUDE = ABS
DRESP = DRESP_DISP_LC12
LE_VALUE = 0.003
END_
OPTIMIZE
ID_NAME = TOPOLOGY_OPTIMIZATION
DV = DESIGN_VARIABLES
OBJ_FUNC = MINIMIZE_VOLUME
CONSTRAINT = MAX_DISP_LC11
DVCON = DVCON_FROZEN
STRATEGY = TOPO_SENSITIVITY
CONSTRAINT = MAX_DISP_LC12
CONSTRAINT = CONSTRAINT_INT_FORCE_ABS
END_
OPT_PARAM
ID_NAME = MY_PARAMETERS
OPTIMIZE = TOPOLOGY_OPTIMIZATION
DENSITY_UPDATE = CONSERVATIVE
STOP_CRITERION_DENSITY = 0.001
END_
|